High speed and efficienct machining of heat resistant alloys
SiC fibers in the material provide strength, flank wear resistance and thermal shock resistance
Features
- Alumina ceramic material with enhanced toughness due to the addition of SiC whiskers
- High-speed machining is possible due to flank and notch wear resistance and toughness
Tooling application
Roughing (no scale) to semi-finishing heat resistant alloys
Turning/Grooving/Milling

| Cutting conditions
Grade | Material | Operation type | Machining | Cutting speed (m/min) | Feed(mm/rev) | DOC(mm) | Coolant |
---|---|---|---|---|---|---|---|
wh03-wh04 | Heat resistant alloys | Turning | Roughing | 180 – 300 | 0.12 – 0.25 | 1.0 – 2.5 | WET |
Profiling / Semi-finishing | 180 – 330 | 0.1 – 0.25 | 1.0 – 2.0 | ||||
Grooving | 0.05 – 0.10 | – | |||||
Milling | Indexable | 600 – 1000 | 0.07 – 0.12 | 1.0 – 2.5 | DRY |
Why are Sialon ceramics so effective at high-speed machining of heat resistant alloys?
Silicon nitride (Si3N4) is combined with Aluminum (Al) and oxygen (O) to make SiAlON.
Sialon has needle-shaped particles similar to that of Silicon nitride.
The arrangement of these particles makes the material withstand the impact force during cutting.
The addition of the alumina improves its heat resistance characteristics.
The property advantages makes it perfect for machining heat resistant alloys.
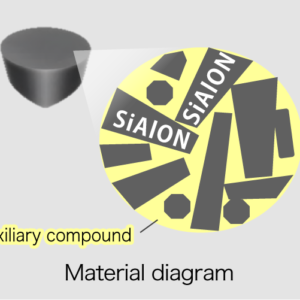
| Whisker ceramic structure

The addition of the silicon carbide (SiC) to alumina greatly improves the strength of material.
Prevents the progression of cracks caused by impact forces during machining.
| Inconel 718 Profiling

[ Cutting conditions ]Material : Inconel718 (Semi-finishing) Cycle time : 5.0 min vc = 240m/min F = 0.15mm/rev ap = 1.0mm, Wet[ Tools used ]Insert used : RPGX120700
| Case Study
Jet engine part | |
---|---|
|
![]() |
|
|
|
|
|
|
|
|
WH04 |
80㎜ / corner (Consistent performance) |
Competitor’s whisker ceramic |
80㎜ / corner (Streaks visible on part surface) |
WH04 had stable machining performance compared to competitor’s whisker grade.
Gas turbine case | |
---|---|
|
![]() |
|
|
|
|
|
|
|
|
WH03 |
1 pass = 2min |
Competitor’s carbide end mill |
1 pass = 60min |
WH03 significantly reduced cycle time compared to the competitor’s carbide end mill.